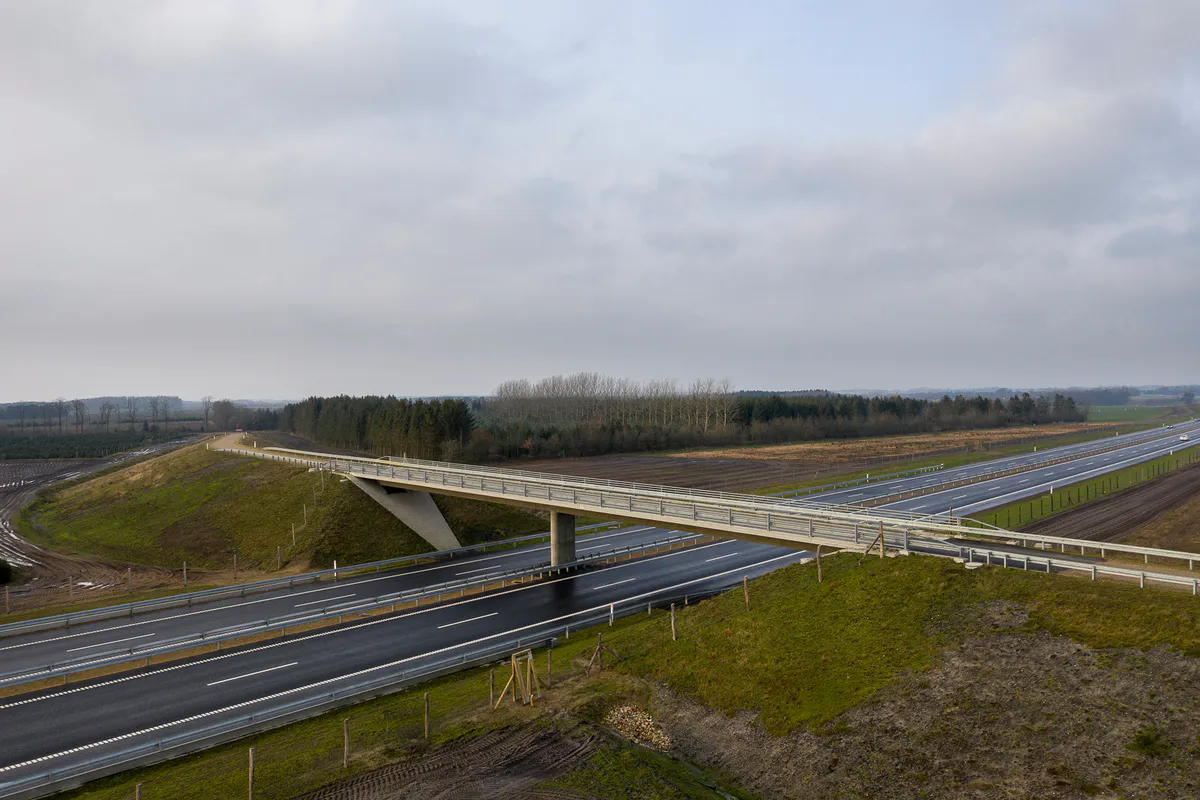
Jernbanebro på strækningen mellem Ringsted og Femern - Kærstrupvej. Foto: Torben Eskerod.
Grøn beton II: Store globale perspektiver i ny CO2 reduceret cement
Beton er verdens vigtigste og mest anvendte byggemateriale, men produktionen af cement står for 5-8 % af den samlede menneskeskabte CO2-udledning, og i 2050 fremskrives behovet for cement og beton til at være dobbelt så stort som i 2010. Reduktion af CO2-udledningen på verdensplan er derfor vigtigere end nogensinde før.
Indlæg af projektleder for innovationskonsortiet Grøn Omstilling af Cement- og Betonproduktion, Lars Nyholm Thrane, Teknologisk Institut
Den danske cementproducent Aalborg Portland A/S har sammen med danske forskere og betonproducenter udviklet en ny type CO2-besparende cement til anvendelse i beton. Arbejdet er udført i Innovationskonsortiet Grøn Omstilling af Cement- og Betonproduktion, der er et fireårigt udviklingsprojekt, som inddrager mange af de vigtigste aktører inden for både forskning, rådgivning og fremstilling af cement og beton i Danmark. Projektet er støttet af Innovationsfonden og har netop afholdt afslutningskonference den 28. februar 2019 på Teknologisk Institut.
Den nye grønne cement kan spare op mod 30 % af den globale CO2-udledning fra cementproduktion. Det er noget, der vil kunne mærkes. I Danmark bygges der årligt broer og bygninger af ca. 8 mio. ton beton, mens forbruget af beton på verdensplan anslås at være 17 mia. ton. På verdensplan vil man kunne reducere CO2-udledningen fra byggeriet med 400 mio. ton om året. Det svarer til den totale årlige CO2-udledning i hele Frankrig.
Ny cement med ler og kalkfiller
Traditionel portlandcement består primært af ca. 90 procent cementklinker, og resten er lige dele kalksten og gips. Udfordringen med den traditionelle type cement er, at produktionen er energikrævende, da råmaterialerne (kridt, sand mm) skal varmes op til ca. 1400°C. Ca. 50 % af CO2udledningen stammer fra selve opvarmningen mens de øvrige 50% stammer fra den kemiske omdannelse af kridt. I Danmark har man haft et lavere CO2-aftryk fra beton, fordi man delvist har brugt flyveaske i stedet for cement til fremstilling af beton. Men flyveaske er et affaldsprodukt fra kulfyrede kraftværker, som er under udfasning. Derfor er det helt afgørende at udvikle alternative cementtyper ikke bare til Danmark, men til et globalt marked.
Den nye grønne cement består af ca. 62 % cementklinker, knapt 17 % kalcineret ler, knapt 17 % kalksten og resten gips, hvilket giver et markant mindre CO₂-aftryk. Det er kombinationen af de tre materialer, der skaber den nye cements gode egenskaber. For at leret opnår de ønskede reaktive egenskaber skal det varmes op til ca. 700-800°C. Det er en langt mindre energikrævende og CO2udledende proces sammenlignet med fremstilling af cementklinker. Globalt set er perspektivet stort, da cementen ikke baserer sig på en knap ressource. Derimod findes ler og kalk i store mængder over hele verden.
Forsøgsprojekt på DTU. Foto: Torben Eskerod.
Fra cement til beton
Cement er en vigtig bestanddel i beton og dens egenskaber har stor betydning for betonens egenskaber. Grøn Beton II projektet har haft stort fokus på at optimere sammensætningen af de nye cementer på en måde, så betonerne opnår egenskaber på niveau med de betoner, som vi kender i dag. Det gælder for styrke og holdbarhed men i lige så høj grad for de produktions- og udførelsesmæssige egenskaber. Det er en kæmpe barriere for implementering af nye grønnere cementtyper, hvis betonerne bliver for klistrede og viskøse. Derfor er der i projektet udviklet en metode for, hvordan man sammensætter betonen med den grønne cement, således at betonen har de samme funktionsegenskaber som traditionelle betoner samtidig med at betonerne er gode og arbejde med i produktionen og på byggepladserne. Metoden, som kaldes for funktionsbaseret design, optimerer ikke alene på betonens tekniske egenskaber men også på betonens samlede CO2 aftryk.
Eksponeringsplads i Hirtshals Havn
Demonstrationsprojekter
Et meget vigtigt omdrejningspunkt for projektet har været at tage betoner med de nye cementer i anvendelse i egentlige bygværker. Disse fysiske aftryk er vigtige resultater fra projektet, og de vil blive fulgt tæt over de næste mange år. Det er her i virkelighedens verden, at betonerne for alvor skal vise deres værd over tid, og resultater og observationer herfra bliver et vigtigt bidrag i forhold til fremtidigt standardiseringsarbejde samt validering af matematiske modeller til at forudsige betons langtidsholdbarhed. Sidstnævnte har DTU arbejdet med og modellerne skal bl.a. kunne bruges til at forudsige transport af klorider fra havvand og ind i betonen, hvilket har afgørende betydning for, hvornår armeringen begynder at ruste.
Betonerne til enkelte bygværker er blevet udviklet og dokumenteret i betonlaboratoriet på Teknologisk Institut. Disse betonrecepter er efterfølgende opskaleret til fuldskala ved betonproducenten Unicon A/S, som har stået for at levere betonerne til alle fire demonstrationsprojekter. De nye cementer er produceret i prøvebatches hos Aalborg Portland. Forud for betonleverancerne har MT Højgaard A/Sgennemført prøvestøbninger med de nye betoner, som har bekræftet, at de både kan produceres og udføres på tilfredsstillende vis, og Rambøll Danmark A/S og Sweco A/S, har været rådgivere på demonstrationsprojekterne.
Vejdirektoratet og Banedanmark har stillet udvalgte konstruktionsdele på tre broer til rådighed for projektet. Vejdirektoratethar været bygherre på broerne, der fører Lindholtvej over Herning-Holstebro motorvejen og Lundgårdsvej over Sydmotorvejen ved Holeby på Lolland. Banedanmark har været bygherre på opførsel af en sideudvidelse af en eksisterende banebro ved Kærstrupvej, også ved Holeby på Lolland. DTU i Lyngby har været bygherre på demonstrationsbyggeriet, hvor et gulv og en væg er blevet støbt i forbindelse med etablering af nye laboratoriefaciliteter på DTU Byg.
I alle fire demonstrationsprojekter er det lykkedes at fremstille og opføre nogle betonkonstruktioner, som duer i praksis og hvor testresultaterne har været tilfredsstillende og som forventet. Målsætningerne for projektet er således opfyldt.
Eksponeringsplads langs Hveens Boulevard. Foto: Torben Eskerod.
Eksponeringspladser
Udover betonerne til bygværkerne har Teknologisk Institut stået for at producere i alt 13 store betonblokke med 8 forskellige betonrecepter, som er blevet placeret på eksponeringspladser i Danmark. Vi har haft mulighed for at benytte de to eksisterende eksponeringspladser i hhv. Rødbyhavn (Femern) og Hirtshals havn, hvor betonemner sænkes delvist ned i havvand. Derudover har vi i samarbejde med Taastrup Kommune etableret en helt ny eksponeringsplads langs Hveens Boulevard, hvor der er tung trafik og saltes om vinteren. Nogle af blokkene er instrumenteret med avanceret overvågningsudstyr, så vi kan opnå meget præcis information om den kloridkoncentration, der skal til for at påbegynde armeringskorrosion, den såkaldte kloridtærskelværdi, som er en af de vigtigste parametre for holdbarheden af anlægskonstruktioner.
De næste skridt
Projektet er nået til vejs ende, og der er skabt et solidt grundlag for anvendelsen af beton med de nye cementtyper. Afslutningen repræsenterer på mange måder også startskuddet til at tage de næste skridt frem mod implementering af de nye cementtyper i dansk betonproduktion. Aalborg Portland A/Sundersøger, hvordan de nye cementtyper kan sættes i industriel produktion. Der er stort spring fra fremstilling af prøvebatches til en kontinuerlig produktion i fuld skala, hvor der skal leveres et produkt, der er konsistent og ensartet i kvalitet. Det kræver en masse overvejelser og ikke mindst betydelige investeringer.
De nye cementtyper er imidlertid ikke tilladt til brug i Danmark. Det kræver derfor at den danske betonstandard bliver revideret. For at få ændret en standard kræver det omfattende dokumentation, og her er der et værdifuldt input fra Grøn Beton II projektet, som er ved at blive overdraget til standardiseringsudvalget.
Endelig ser Vejdirektoratet og Banedanmark på, hvordan de kan indarbejde krav til de miljømæssige forhold i forbindelse med udbud og vejregler. Det vil bl.a. basere sig på det analysearbejde, der er gennemført i projektet, hvor der fx er set på de LCA systemer, der anvendes i udlandet. I forhold til byggeriet, så findes der allerede flere systemer til vurdering af bæredygtigheden bl.a. DGNB. Projektets arbejde har vist, at beton med reduceret miljøaftryk har ganske stor betydning for den samlede DGNB score.
Eksponeringsplads i Rødby Havn
Deltagerne i innovationskonsortiet
Deltagerne i innovationskonsortiet er Teknologisk Institut (projektleder), Aalborg Portland A/S, Dansk Beton Fabriksbetongruppen, Unicon A/S, Sweco A/S, Rambøll Danmark A/S, MT Højgaard A/S, Banedanmark, Vejdirektoratet, Femern A/S, Energistyrelsen, DTU Byg, Erhvervsakademiet Lillebælt, Københavns Erhvervsakademi, Via University College, Erhvervsakademi Sjælland og Center for Betonuddannelse.