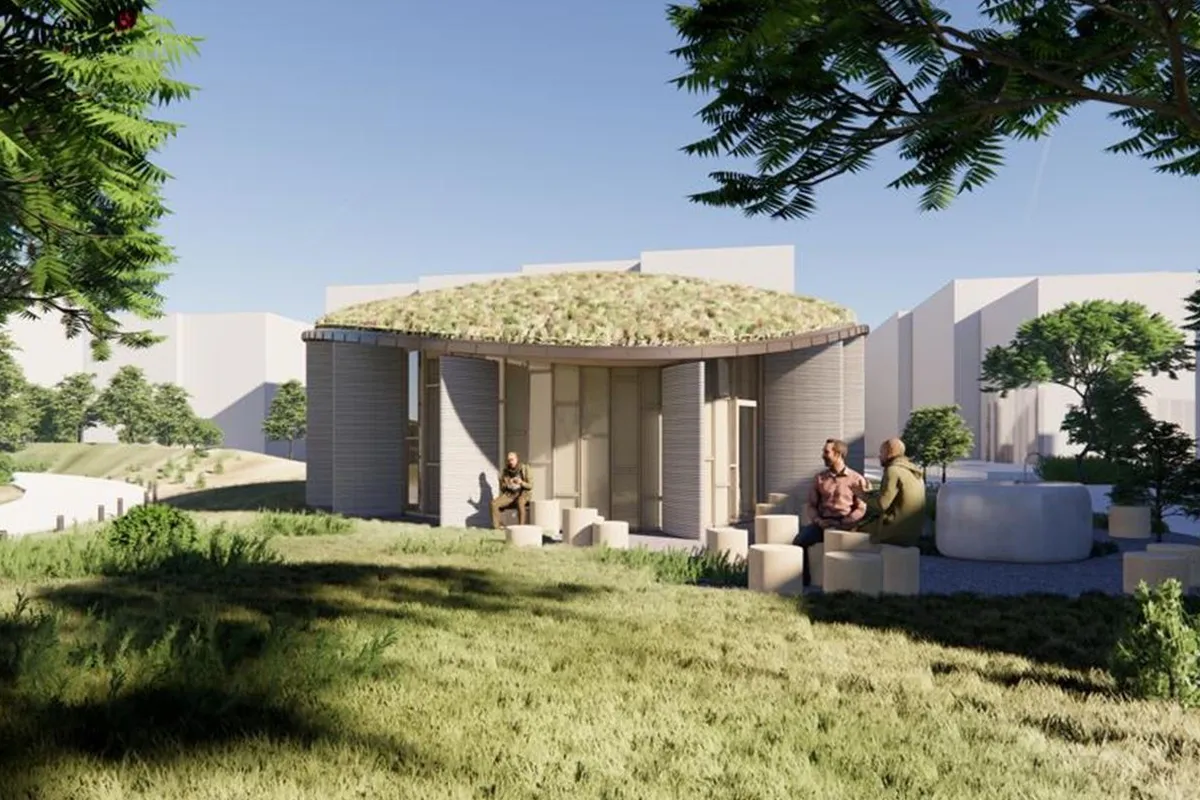
Rendering af Henning Larsen Architects, som viser Fælleshuset i Kanalbyen, Fredericia
Innovationsprojekt viser muligheder for at sænke betons CO2-udledning
Teknologisk Institut er sammen med en række aktører gået med i et innovationsprojekt, som skal sænke CO2-aftrykket for byggeri markant. De første resultater fra laboratoriet ser lovende ud, og de forskellige løsninger vil blive samlet i showcase-byggeriet Fælleshuset i Kanalbyen i Fredericia.
Innovationsprojektet om at nedbringe CO2-udledningen fra beton er støttet af Realdania, og ud over Teknologisk Institut deltager AP Ejendomme, Henning Larsen, Rambøll, Dansk Beton, Unicon og Aalborg Portland.
Det kommende fælles- og aktivitetshus bliver en del af Kanalbyen, en nylig opført bydel med moderne boliger, kanaler og natur, som ligger mellem Lillebælt og Fredericias bycentrum. Udover at det nye fælles- og aktivitetshus, skal fungere som samlingspunkt for forskellige brugergrupper, skal det også være showcase for nye og bæredygtige teknologier. Forud for selve byggeriet, arbejder Teknologisk Instituts eksperter på det omfattende prøvningsprogram, som er forbundet med byggeriet, og Thomas Juul Andersen fra Teknologisk Institut fortæller, at de første resultater ser lovende ud:
- I projektet arbejder vi med flere innovative løsninger for at kunne opnå det ambitiøse mål for CO2-aftrykket. En af de metoder, vi har taget i brug, er 3D printet beton til de 3 meter høje, bærende søjler. Brugen af 3D print gør, at søjlerne kan laves hule frem for traditionelle, massive søjler, hvilket medfører en betydelig materialebesparelse. Herudover bruges der et beton mix-design, som indeholder både FUTURECEM og flyveaske for at opnå en så lav CO2-udledning fra råmaterialerne som muligt.
Målet er at opføre et hus med beton som det primære materiale med et CO2-aftryk på mindre end 5 kg CO2/m2/år for en 50-årig periode. Det kræver selvsagt innovative løsninger, hvis det skal lykkes at reducere CO2-aftrykket så markant.
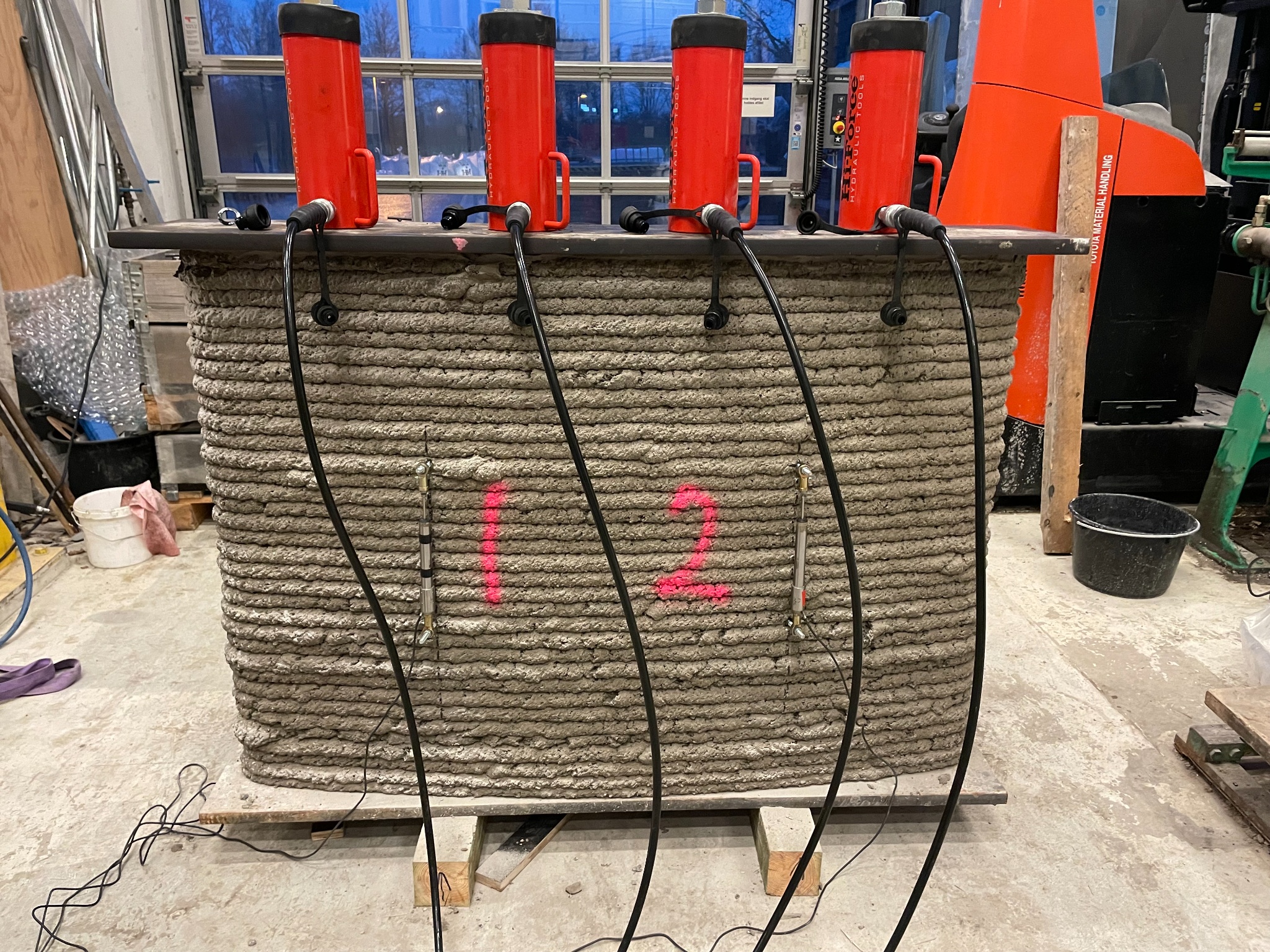
3D print klarede testen
Når der arbejdes med nye og innovative løsninger, som ligger uden for de gældende normer, er det vigtigt, at der udføres omfattende dokumentation for kvalitet og holdbarhed. Derfor er flere forskellige typer af betonelementer blevet printet i samarbejde med COBOD og 3DCP Group med et mix-design udviklet af Teknologisk Institut med et CO2-aftryk på omkring 200 kg CO2/m3. Efter hærdning er alle elementer fragtet til Teknologisk Institut til prøvning og dokumentation i betoncenterets testlaboratorie.
- Testprogrammet omfatter blandt andet tests af 1m høje søjleudsnit, hvilket har krævet en hydraulisk løsning af test-setup’et, hvor olie manuelt pumpes ind i fire 33 tons donkrafte, indtil der tilsammen opnås et tryk på ca. 1300kN, hvilket er langt over design-værdien, fortæller Nina Marie Sigvardsen fra Teknologisk Institut og tilføjer, at alle søjlestykkerne klarede testen uden at få hverken brud eller revner.
For at kunne dokumentere, hvor meget de printede søjler rent faktisk kan holde til, blev der også testet tyve 3D-printede, hule cylindere med en ydre diameter på 0,4m og en højde på 1meter – vel at mærke ud over de sædvanlige tryk af solide cylindere, støbt af beton taget direkte fra 3D printerens dysse.
- Disse tests krævede, at vi tog vores største trykpresse i brug og adviserede kollegaerne om, at de ikke skulle tage sig af de høje brag fra hallen. Alle test – hule såvel som solide cylindere – viste også styrker over den forventede design-værdi, forklarer Nina Marie Sigvardsen.